Understanding FDM 3D Printing: A Comprehensive Guide for Businesses
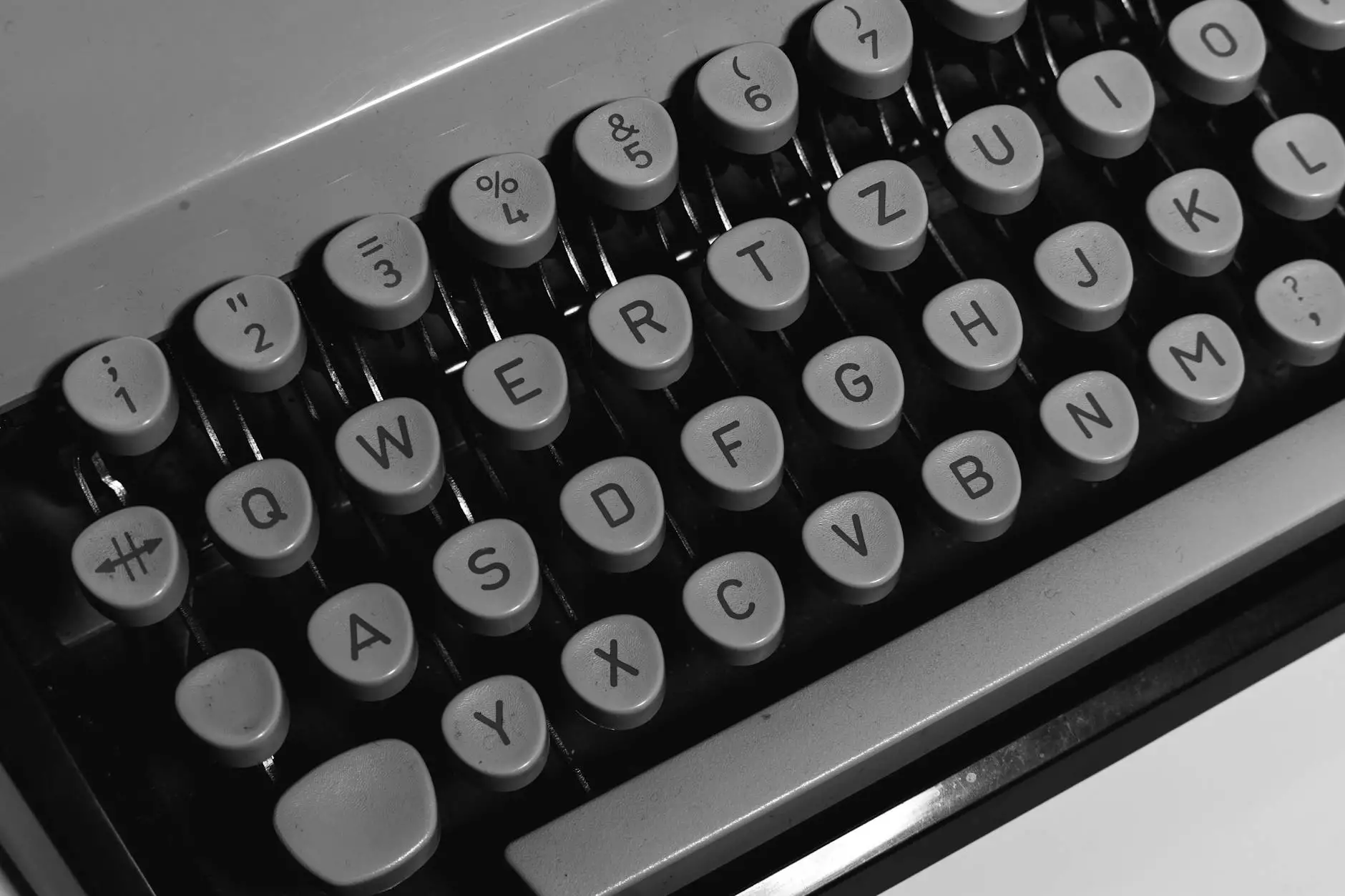
Fused Deposition Modeling (FDM), predominantly known as FDM, is one of the most popular and widely used methods of 3D printing. With a significant impact on the way businesses operate, FDM 3D printing provides a variety of applications that can streamline workflows, enhance product development, and vastly reduce costs. In this article, we will delve into the ins and outs of FDM technology, exploring its many advantages, diverse applications, and tips for leveraging it in your business strategy.
What is FDM 3D Printing?
FDM is a 3D printing technology that creates three-dimensional objects by layering materials. The process begins with a 3D model created in CAD (Computer-Aided Design) software. This model is sliced into countless horizontal layers, which the FDM printer builds layer by layer using thermoplastic materials.
The FDM Process
- 3D Modeling: Design your part in a CAD software.
- Slicing: The model is sliced into layers with slicing software.
- Printing: The printer extrudes melted thermoplastic filament, depositing it layer by layer.
- Cooling: Each layer cools and solidifies to create a rigid structure.
Advantages of FDM 3D Printing
FDM 3D printing has revolutionized the manufacturing landscape, offering numerous advantages for businesses, including:
Cost-Effectiveness
Reduction in Material Waste: FDM utilizes thermoplastic materials, creating parts with minimal waste. Traditional manufacturing methods often result in significant scrap material, but FDM's additive process builds parts layer by layer.
Lower Production Costs: 3D printing eliminates complex tooling and production setups, allowing businesses to save money in the early stages of development.
Versatility of Materials
FDM supports a wide range of thermoplastic materials, such as:
- ABS (Acrylonitrile Butadiene Styrene)
- PLA (Polylactic Acid)
- PETG (Polyethylene Terephthalate Glycol)
- Nylons and composites
Speed and Efficiency
FDM allows for rapid prototyping, enabling businesses to transform ideas into physical products within hours or days. This speed significantly accelerates the product development life cycle, allowing for quicker testing and iteration.
Customization and Complexity
With FDM technology, businesses can create customized parts that meet specific functional or aesthetic requirements. Complex geometries that would be challenging or impossible to produce with traditional manufacturing methods can be achieved with ease.
Applications of FDM in Business
FDM technology can be applied across diverse sectors, including:
Aerospace
In the aerospace industry, FDM printing is utilized to create lightweight parts and components that withstand high temperatures and stresses.
Automotive
The automotive sector uses FDM technology for prototyping parts, tooling, and even producing end-use components, which contribute to the light-weighting trends in vehicle design.
Consumer Goods
From custom phone cases to designer toys, businesses in the consumer goods market leverage FDM to create unique, tailored products.
Healthcare
In healthcare, FDM facilitates the production of customized prosthetics, dental models, and even surgical instruments, enhancing patient care and outcomes.
Implementing FDM in Your Business
If you are considering integrating FDM technology into your business operations, here are some steps to guide you through the process:
1. Assess Your Needs
Evaluate your current production processes and identify areas where FDM could be beneficial, such as rapid prototyping, custom tooling, or small-batch production.
2. Choose the Right Equipment
Investing in a high-quality FDM printer is crucial. Consider factors such as:
- Build volume
- Material compatibility
- Print speed
- Reliability and user reviews
3. Train Your Team
Provide training for your staff to ensure they are proficient in using FDM technology and can troubleshoot common issues.
4. Integrate with CAD Software
Ensure you have the necessary software for designing and slicing models as well as software for managing print jobs efficiently.
Challenges and Considerations
While FDM offers numerous advantages, there are challenges that businesses should consider:
Material Limitations
Although FDM supports various thermoplastics, each material has unique properties that may limit its application in certain environments. Ensure the material chosen meets the specific requirements of your product.
Post-Processing Needs
Many FDM prints may require post-processing, such as sanding or painting, to achieve the desired finish.
Print Quality
Factors such as printer calibration and environmental conditions can affect print quality. Regular maintenance and monitoring are essential for consistent outputs.
Future Trends in FDM Technology
The future of FDM technology looks bright, with several emerging trends that may impact the way businesses utilize 3D printing:
Increased Material Variety
Researchers are continuously developing new thermoplastic materials, expanding the applications and performance capabilities of FDM printing.
Integration with AI and Automation
Artificial intelligence and automation will further streamline FDM processes, improving efficiency, consistency, and reducing the likelihood of errors during printing.
Sustainability Focus
As businesses strive to reduce their environmental impact, the development of biodegradable and recyclable materials for FDM printing is expected to gain significant traction.
Conclusion
Fused Deposition Modeling (FDM) is transforming the landscape of manufacturing and prototyping across industries. The myriad of applications, combined with its cost-effectiveness and flexibility, makes FDM an invaluable tool for businesses aiming to innovate and lead in their respective markets.
If you are looking to explore the capabilities of FDM 3D printing, Infotron (infotron.com.tr) is here to support you with the knowledge and tools you need to succeed. Embrace the future of manufacturing and unlock your business's potential with FDM technology!